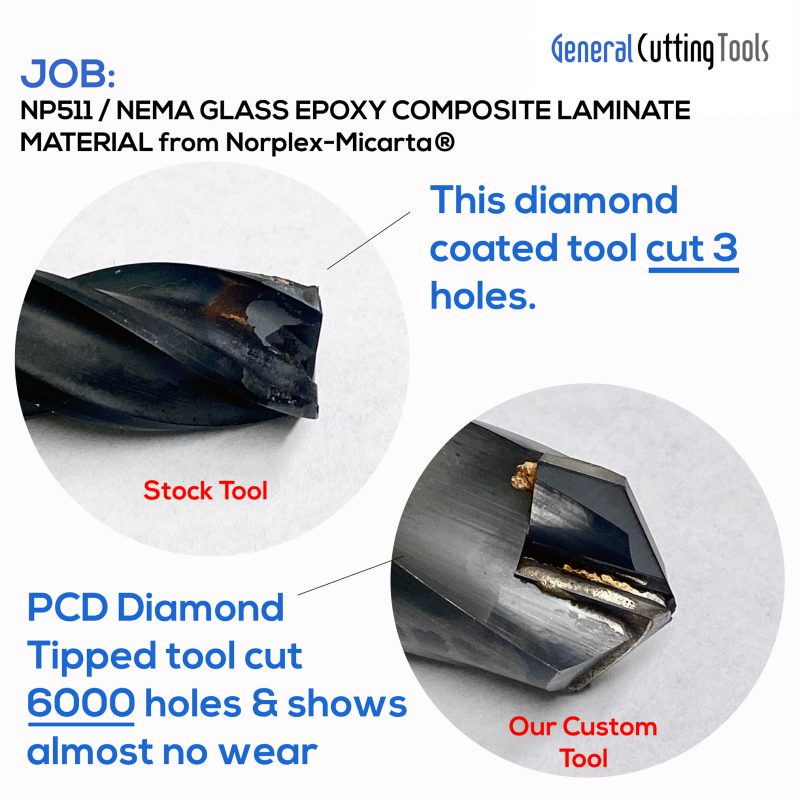
Diamond Drills for Composites: The Power of Precision and Durability
The world of composites is expansive and ever-evolving. As materials get tougher, the tools to handle them need to evolve as well. One such tool that has proven its mettle in recent years is the diamond drill. Famed for their durability, sharpness, and precision, diamond drills have found their way into a myriad of applications, and the realm of composite laminates is no exception.
Understanding Composites: NP511 (NEMA G-11) GLASS EPOXY COMPOSITE LAMINATE MATERIAL
Before diving into the efficacy of diamond drills, it’s essential to understand the material at hand. The NP511 (NEMA G-11) Glass Epoxy Composite Laminate is a high-temperature, high-strength material used in a variety of electrical applications. Characterized by its excellent electrical properties and chemical resistance, this composite is challenging to machine due to its fibrous nature and hardness. Enter the diamond drill.
General Cutting Tools’ Success Story
A real-world application can best demonstrate the prowess of diamond drills. General Cutting Tools, a renowned player in the tool industry, recently showcased the capability of their PCD diamond tipped tool on the NP511 (NEMA G-11) material.
For a customer project, General Cutting Tools was presented with the task of drilling through the NP511 (NEMA G-11) composite. Using a conventional diamond coated tool, only three holes could be drilled before the tool met its limit. However, the performance of the PCD (Polycrystalline Diamond) Tipped tool was nothing short of spectacular. Out tool managed to drill a whopping 6000 holes and, astonishingly, showed almost no signs of wear.
Why are Diamond Drills Effective?
The phenomenal success of the PCD Diamond Tipped tool in this instance can be attributed to several reasons:
- Hardness & Durability: Diamond is the hardest known material on Earth. This hardness translates to a sharp cutting edge, which is maintained over prolonged usage. PCD tips have a high wear resistance, ensuring a longer tool life.
- Precision: Diamond drills offer a higher level of precision compared to their counterparts. Their sharpness ensures clean cuts, especially crucial for materials like the NP511 (NEMA G-11) composite that demand accuracy.
- Reduced Heat Generation: The high thermal conductivity of diamond drills dissipates heat effectively, reducing the chances of material damage or tool degradation.
- Cost-Efficiency: While the initial investment in diamond tools may be higher, their longevity and performance ensure cost savings in the long run. In applications where thousands of holes are needed, like the one presented by General Cutting Tools, the cost per hole is significantly reduced.
The example provided by General Cutting Tools underscores the value of diamond drills, especially in handling tough composite materials. As industries demand better performance, longer tool life, and cost-effective solutions, diamond drills, particularly those with PCD tips, are set to shine even brighter in the machining landscape. Whether it’s the NP511 (NEMA G-11) composite laminate or any other challenging material, diamond drills prove that they are more than up to the task.